Product cooling processes occur in a wide range of industries. Factors such as cooler dimensions, retention times, cooling air volumes as well as moisture evaporation play a major role in the cooling process. Changing these parameters can have a major impact on the end product. Compared to dryers, for example, the cooling process is even more dependent on the product features and conditions of the ingoing air. Small changes can have a major impact on cooling and moisture management.
AirRotec has many years of experience in designing and optimising cooling processes.
Cooling processes | Common problems and possible solutions
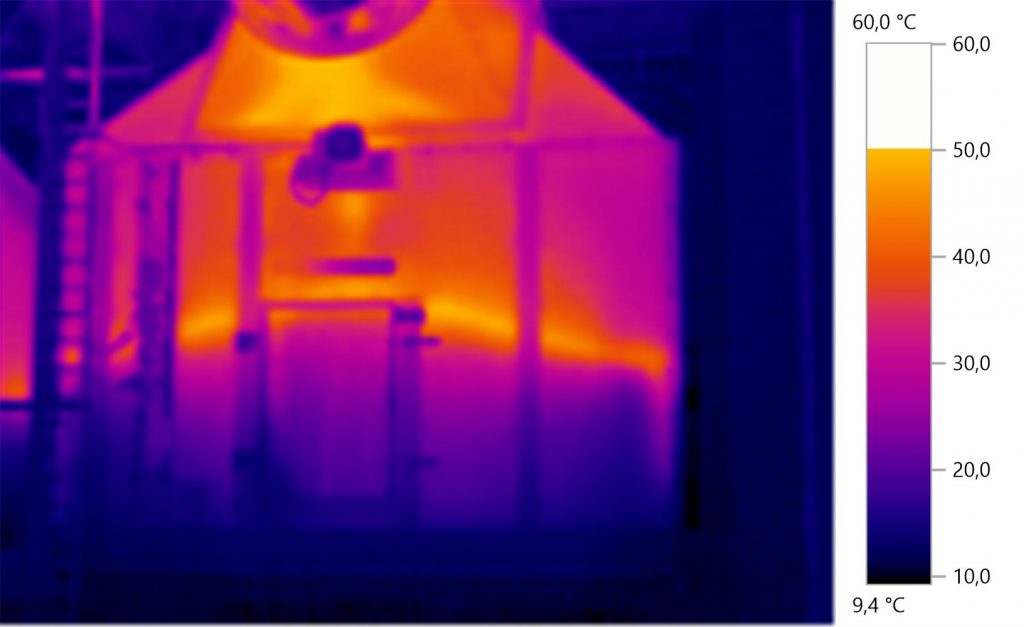
Common challenges with cooling processes:
- The end product isn’t cold enough
- Part of the product is cooled less or poorly (hotspots)
- The product is being drawn into the exhaust
- The cyclone outlet becomes blocked
- The filters are quick to become dirty
- Change over time is too long
- The product has a critical shelf life (due to the formation of fungi)
- Coordination size of the cooler and air exhaust filter when production capacity increases
How can you optimise a cooling process? A number of ideas:
- If you configure the cooling process and balance between retention time and air volume differently, it will affect the moisture content of the end product
- If you want to change product faster, there are various options where you don’t need to make any alterations to existing coolers. Improve changeover time without installing an intermediate gate from a counter-flow cooler, for example.
- Prevent air leaks in the cooler that cause cold bridges, the forming of condensation and dirt
- Prevent significant differences in temperature between storage and the product. Products that are stored in warm conditions have a shorter shelf life.
AirRotec is able to offer help with all these and other questions about cooling processes.
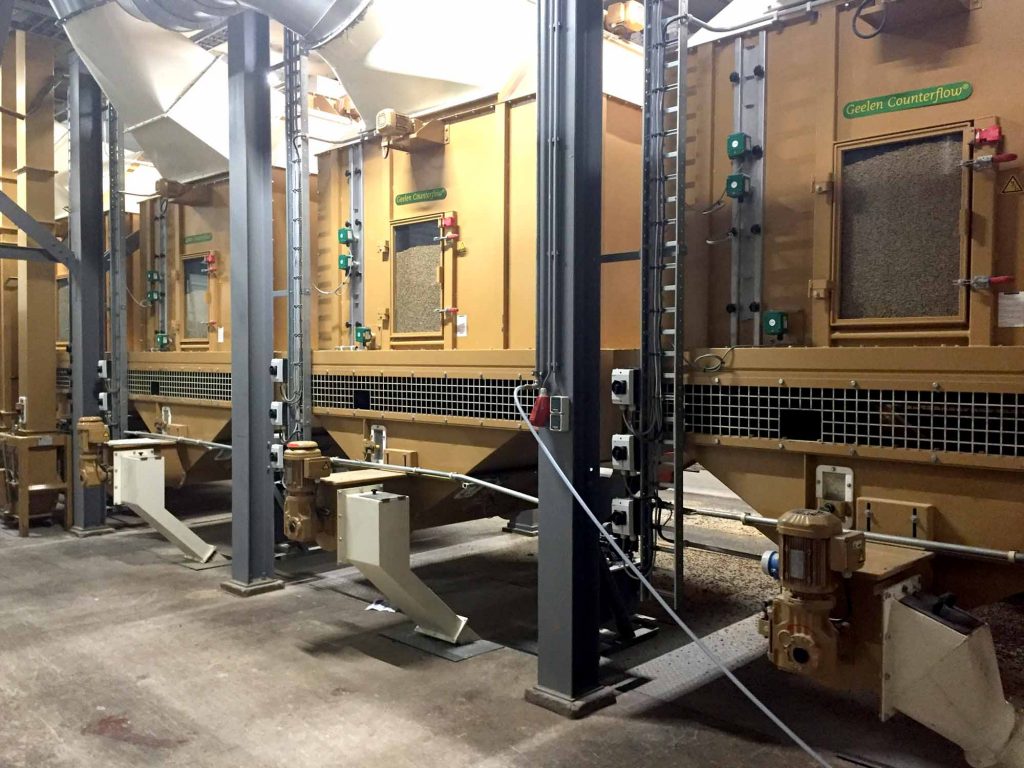